Here are a few interesting things I’ve turned in the last couple months from wet wood. Two are complete, a couple are just rough turns.
Let’s start with the cherry that was cut down last October. Fortunately, we cut the logs longer than necessary. So although I have to take off quite a few inches from either end because they’ve cracked over the months, I do still get to good wood for more rough turned cherry bowls and platters. But what to do with the little bits left after I fussy cut for the big stuff?
Here’s one thing I tried. (Sorry I have limited photos of the process.) I had a slice of log about 2-3 inches thick. So I decided to try my hand at a cross grain tube, something I’ve seen Richard Raffan make. It’s actually quite a fun little project. I cut a spindle blank from just to the side of the pith. This gets mounted just like you’d mount a stick to turn a rolling pin, or ornaments.
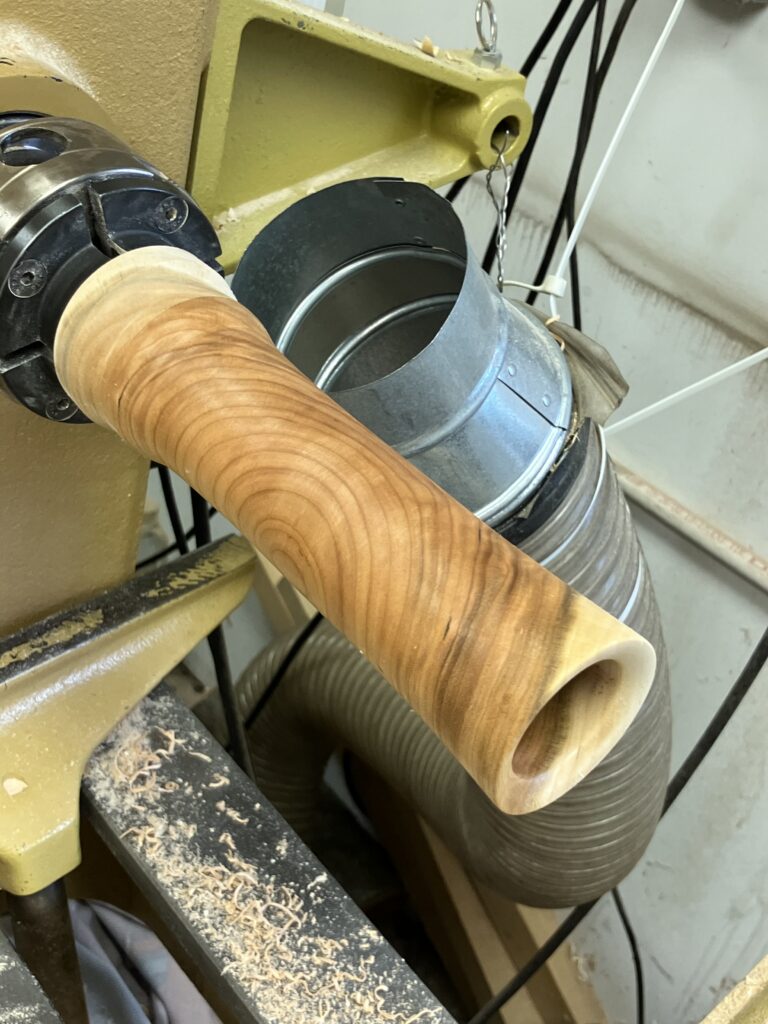
But what’s different is that the grain is running in the same direction it would if it were a bowl. The grain is running the short way across the stick, not the length of the stick like it would be for a rolling pin. So you’re cutting a spindle, but because of the direction of the grain (across the piece, thus “cross grain tube”), you use bowl gouges. I didn’t find it technically challenging–it just reinforced in me that the wood determines the tool just as much as the shape.
Here it is just after it was turned, before it dried and warped and before I put any finish on it. (Keep reading for a photo of the final product.)
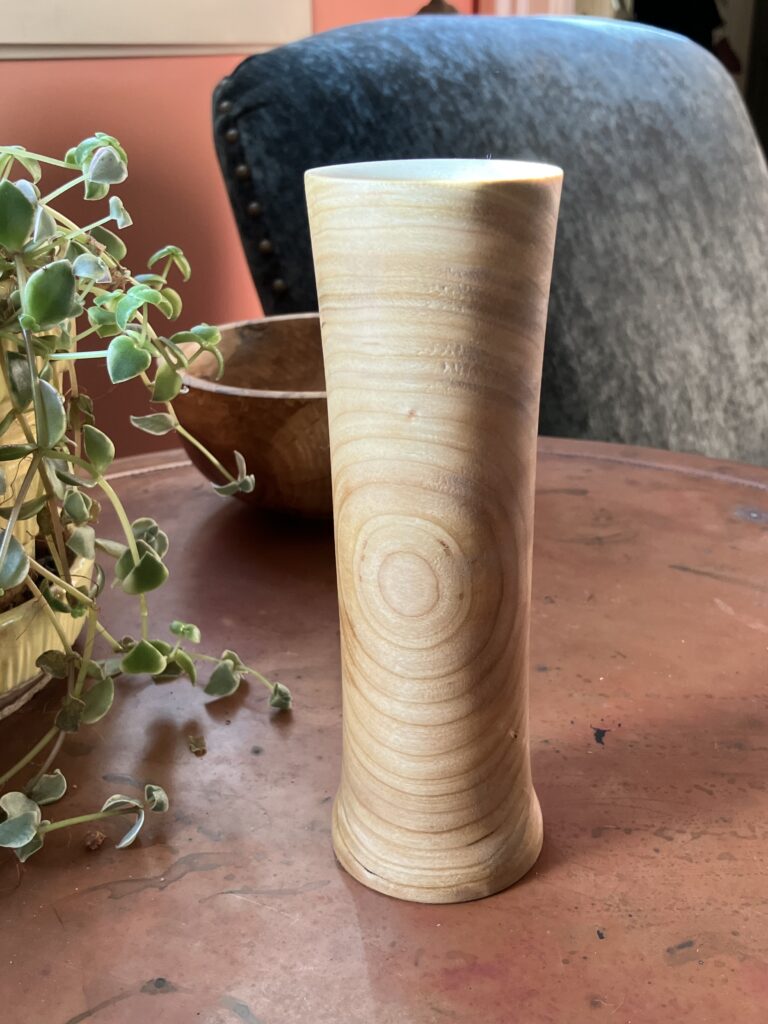
The next day, I took this scrap
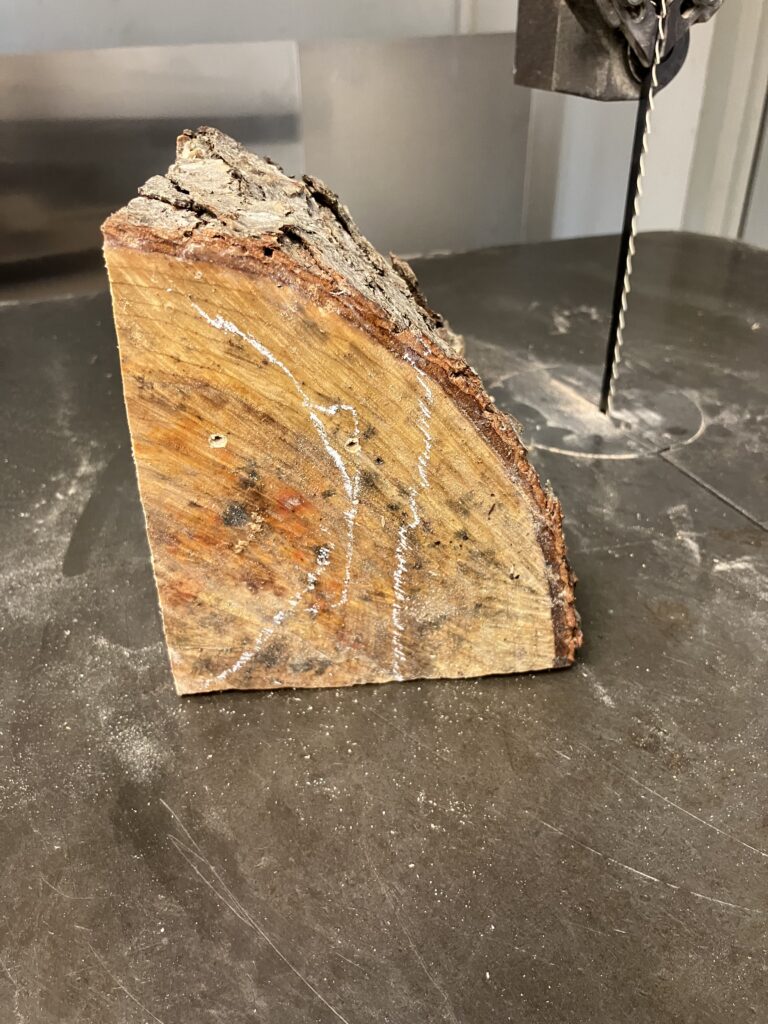
…and turned this. I was REALLY happy with this. Finally figuring out how to do this was such a great feeling.
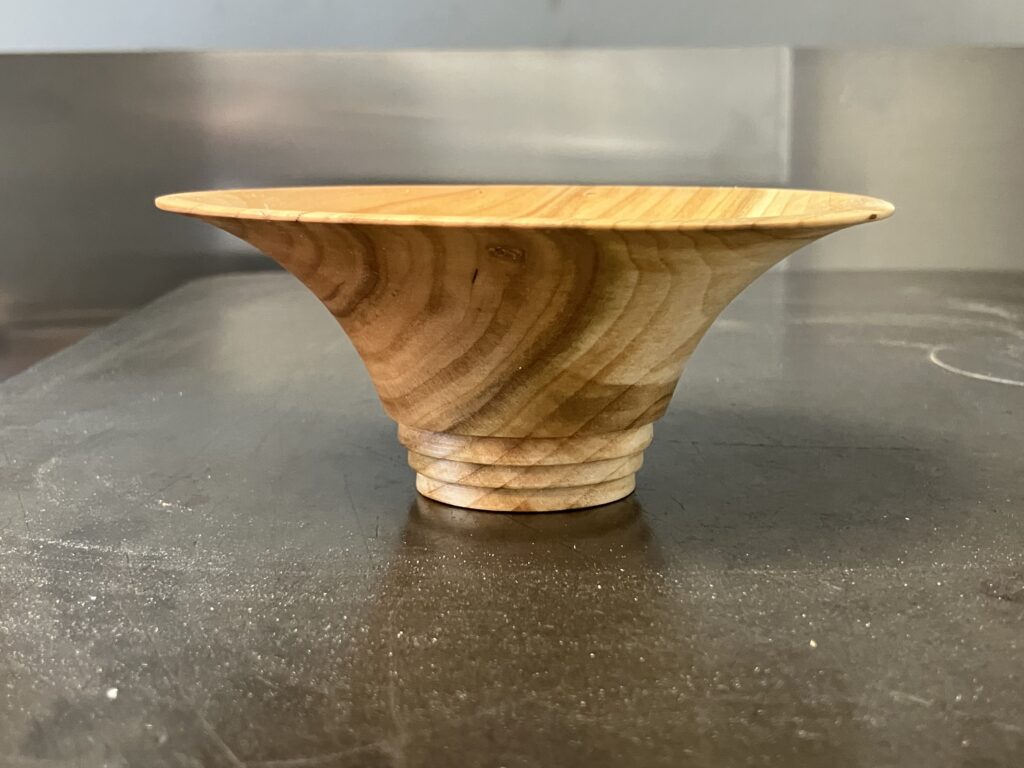
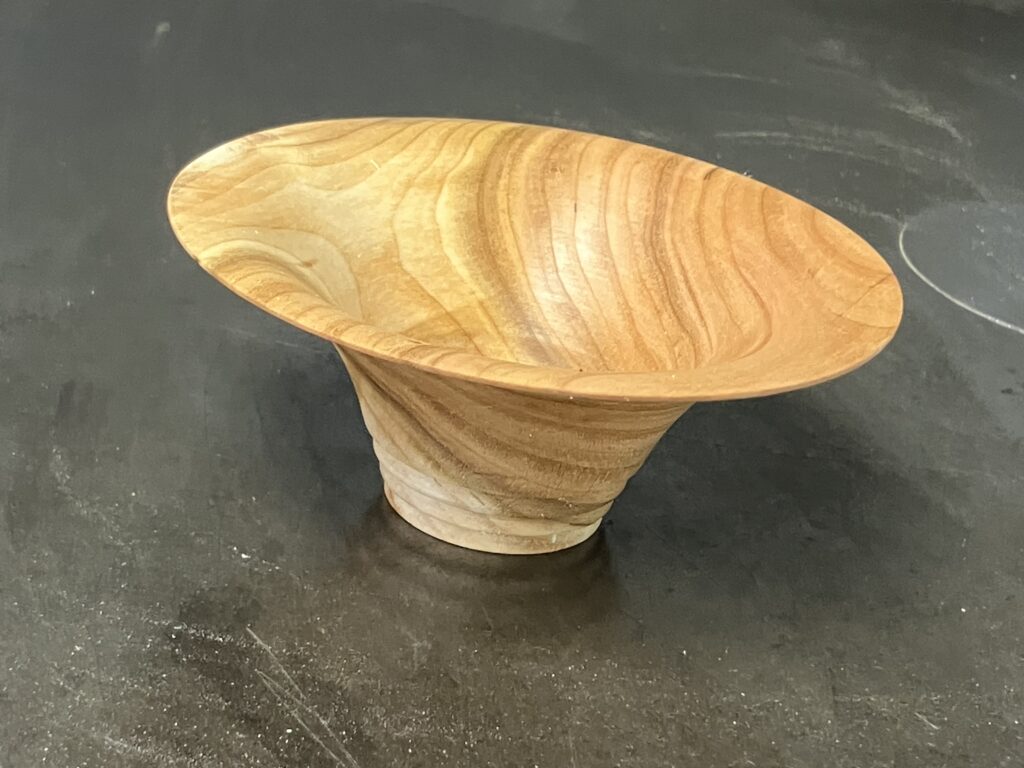
Here are the pair, all dried and warped and finished and beautiful
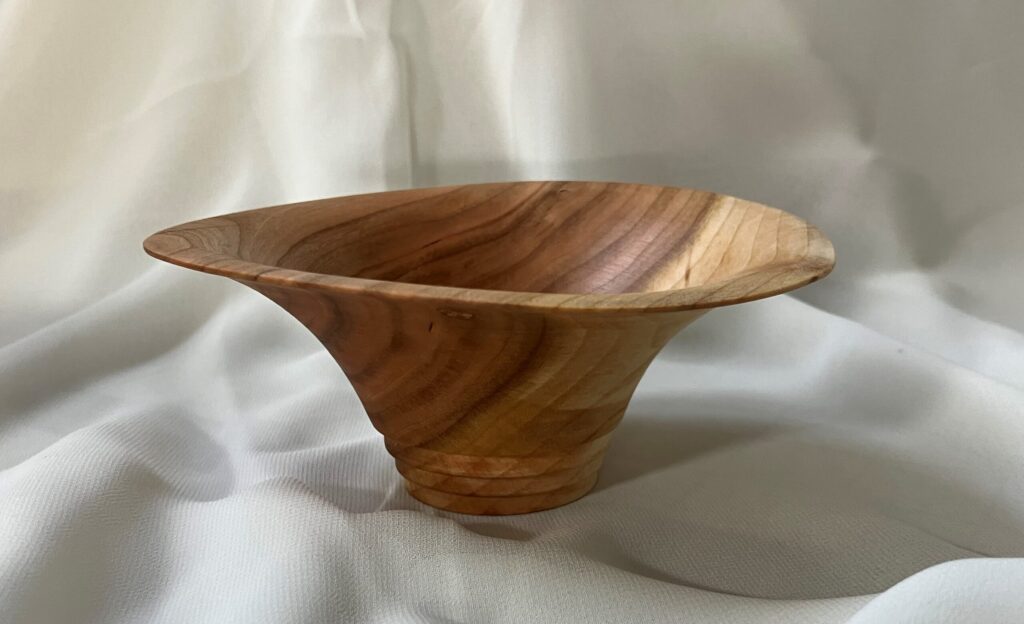
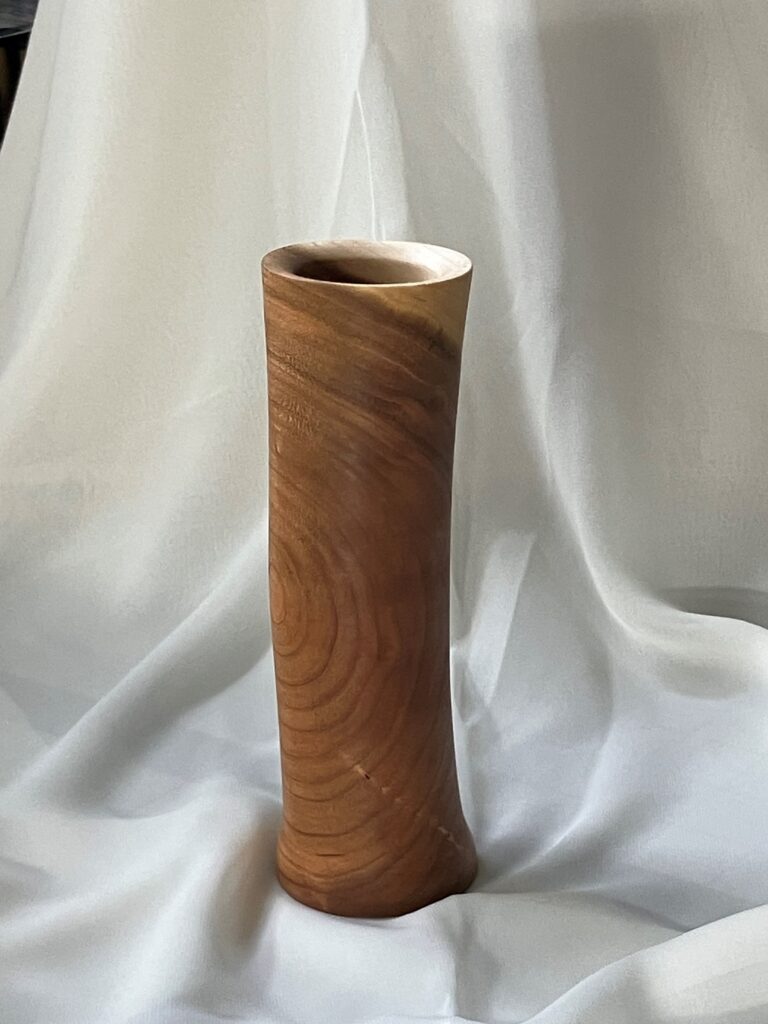
Before I close this post, I wanted to share some last bit of rough turned maple. Another crotch from the maple from July 2023
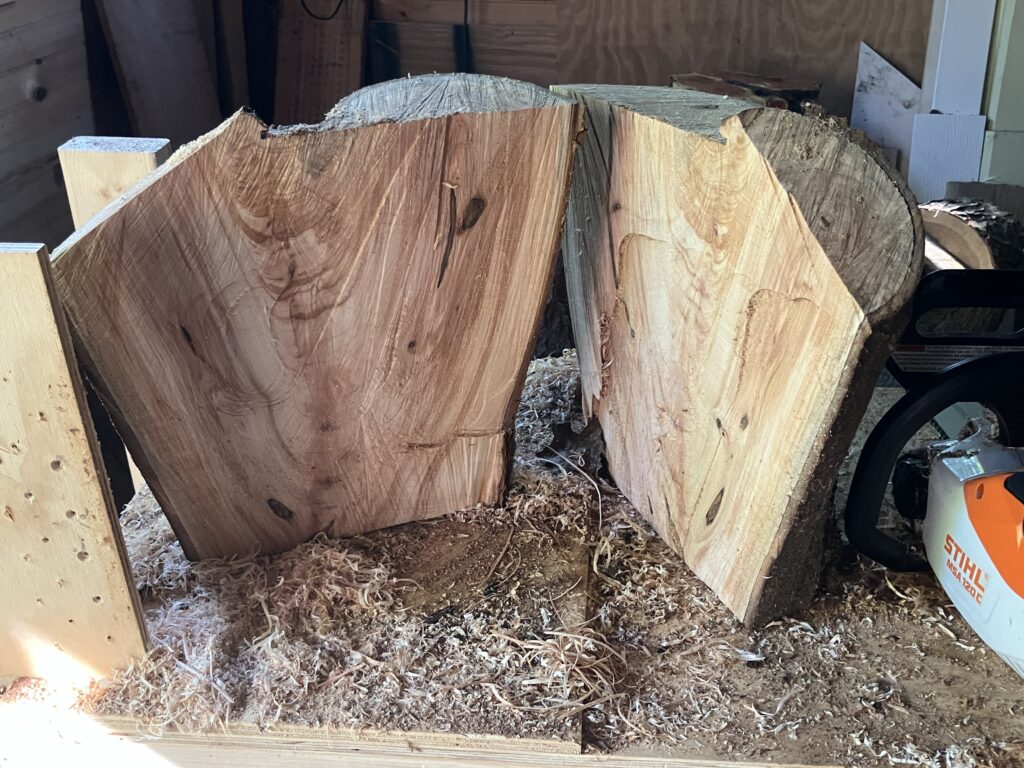
I made what I hope will be a matched pair of bowl and platter
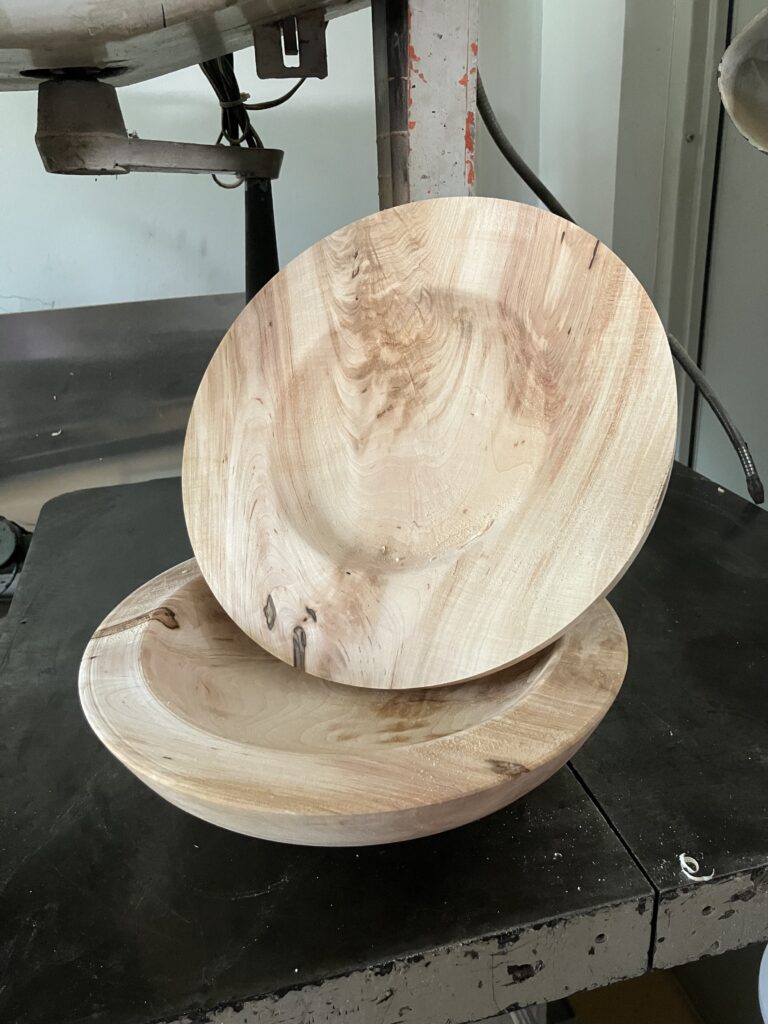